- Home
- Sustainability
- Social
- Employees
- Occupational Health and Safety
Occupational Health and Safety
We aim to create safe working environments by adopting a Health and Safety Management Policy each fiscal year, and by sharing our philosophy on occupational health and safety with employees.
Basic Policy on Health and Safety Management
Our goal under the Health and Safety Management Policy is to achieve a continual reduction in accidents. We are achieving this by maintaining a PDCA cycle in which accidents are analyzed each year in order to identify issues so that countermeasures can be included in the Health and Safety Management Policy for the following fiscal year.
The Health and Safety Management Policy includes both our basic policy and priority action items. It is reported to senior management after deliberations by the Health and Safety Management Committee.
Basic Policy on Health and Safety Management
We put the health and safety of employees first.
Accidents can and must be prevented.
Our managers and supervisors are constantly working to prevent industrial accidents by using risk assessments to detect and eliminate safety-related issues with machinery and equipment. We also use risk prediction activities to prevent unsafe behavior by workers and create safe working environments.
We are working to prevent traffic accidents by providing road safety and hazard prediction training, especially for young employees and older workers. We are also enhancing our road safety guidance activities in order to prevent accidents while walking or operating vehicles, including bicycles, en route to or from work.
Through our health management initiatives, we are helping to enhance the physical and mental health of our employees, and to maintain and enhance work environments that are safe, comfortable, and hygienic.
Individual employees help to eliminate unsafe behavior by raising their awareness of potential hazards. They are also working to maintain and improve their mental and physical health.
Priority action items
Occupational accidents
- Raise awareness about hazards by entrenching the practice of reporting near-miss incidents, implementing countermeasures, and sharing information.
- Increase opportunities for hazard prediction training, instill the habits of pre-work hazard prediction and pointing and calling, and eliminate unsafe behaviors.
- Create workplace environments that are not conducive to accidents by systematically implementing risk assessment activities (including for hazardous chemical substances).
- Monitor the risk status of chemicals handled using safety data sheets and other means, and provide thorough safety education.
- Ensure that equipment is consistently turned off during cleaning or when malfunctions occur, alongside the strengthening of measures (such as the use of safety covers) to prevent entanglement in machines.
- Prevent disasters by maintaining and strengthening the 5S methodology—seiri, seiton, seiso, seiketsu, shitsuke (usually translated into English as “sorting, setting in order, shining, standardizing, and sustaining”)—in the workplace.
- Share information about accidents that have occurred within the Nisshin Seifun Group in order to prevent recurrences of similar accidents.
- Increase safety educational opportunities for older workers (in their 50s and older) and ensure that education is carried out thoroughly.
(Ensure the safety of older workers by promoting the utilization of Age Action 100*1 and the Age-Friendly Guidelines.*2) - Strengthen measures to prevent tripping, trapping and entanglement accidents and cutting and grazing accidents. To prevent tripping accidents in particular, modify equipment and facilities, such as the installation of non-slip sheeting, and the redesign of floors and grating to prevent slipping.
- Provide safety education for foreign employees.
- *1 Compiled by the Japan Industrial Safety and Health Association, Age Action 100 is a set of workplace improvement tools based on a 100-item checklist that is used to review work methods and develop good working environments for older workers.
- *2 The Age-Friendly Guidelines were formulated by Japan’s Ministry of Health, Labour, and Welfare with the aim of creating safe, pleasant working environments for older workers. They consist of items that require action by businesses and workers.
Traffic accidents
- Continually raise awareness of the importance of anticipatory driving.
- Raise hazard awareness through regular hazard prediction training based on the use of hazard prediction videos and traffic accident news items.
- Ensure that a safe distance is maintained from the vehicle ahead whether moving or stationary (e.g., a gap of at least 2 seconds, depending on the speed of travel, a distance from which the lower edge of the rear bumper of the vehicle ahead is visible when stopped at an intersection).
- Check safety, especially at key locations, including intersections or parking lots (such as by pointing and calling).
- Improve the driving skills of workers under 30 (e.g., instruction by an accompanying supervisor, attendance at an outside driving school).
- Install safety devices, driver support systems, and dashboard camera in commercial vehicles.
- Set schedules and encourage behavior that provide ample time.
- Respond to amendments of the Japanese Road Traffic Act (such as introducing alcohol checks).
- Identify potential hazards (including natural disaster risks) along routes used by workers who commute by car or other means and share hazard information at business sites and in workplaces.
- Provide thorough traffic safety training for young workers aged under 30 and senior workers aged 50 and older.
- Expand multilingual traffic safety guidance for foreign employees.
- We remind people that when crossing roads on foot, even if the light is green, they need to check for vehicles running red lights from left or right. We also raise awareness of the need to enhance their visibility to drivers when walking at night, such as by wearing bright clothing or carrying a light.
- Take steps to prevent self-inflicted accidents.
For example, we alert people to the ban on engaging in other activities, such as talking or looking at smartphones, while cycling or walking. We also encourage people to look out for hazards, such as gutters and uneven ground, while traveling to and from work on foot or by bicycle.
* Natural disaster risks include road blockages due to landslides, rising river levels, and other consequences of earthquakes, typhoons, and rainstorms, etc.
Measures to prevent minor and major fires
- Regularly inspect equipment, such as heating and cooking apparatus (especially friers), and ensure that surrounding areas are kept clean, including exhaust ducts.
- Ensure that all workers, including staff of outsourcing contractors, are aware of and comply with the smoking rules.
- Strictly limit and control the use of fire through regulations.
- Ensure that hazardous materials, designated combustibles, and waste at construction sites and at other locations are stored and managed in the correct places and using the appropriate methods in accordance with regulatory requirements.
Health management
- Comprehensively implement and improve countermeasures against infectious diseases in the workplace.
(Examples: Monitoring of CO2 levels to ensure that ventilation systems are working properly, measures to prevent heat stroke when workers are wearing masks, improvement of hand-washing and disinfection equipment) - Review occupational health and safety management frameworks.
(E.g., Notify Labour Standards Inspection Offices of the appointment of sanitation managers, safety managers, industrial physicians, and overall health and safety management supervisors. Ensure that changes to the operations and administration of health and safety committees are properly implemented. Carry out inspection tours by industrial physicians and sanitation managers) - Reliably track the implementation of health checks, provide health guidance, and make effective use of health check the results (from a health management perspective).
- Operate a stress check system and implement primary prevention and workplace improvement measures.
- Pursue occupational health management on three levels (work management, workplace management, health management).
- Monitor required environmental conditions and eliminate health hazards in working environments (e.g., prevention of heat exhaustion, noise countermeasures, ventilation of areas where hazardous solvents and other chemicals are used).
- Reduce long working hours and total working hours.
- Implement health initiatives (e.g., health seminars).
Targets for FY 2025
Zero occupational accidents in the workplace
Zero traffic accidents caused by Nisshin Seifun Group personnel
Zero long-term absences due to workplace accidents
Zero minor or major fires
Occupational health and safety management
Our initiatives to enhance our health and safety management systems include the establishment of a Health and Safety Management Committee made up of group company directors with production-related responsibilities, under the chairmanship of the Nisshin Seifun Group Inc. Director and Managing Executive Officer of the Technology and Engineering Division. We also created a Safety and Hygiene Management Office within the Technology and Engineering Division. The Health and Safety Management Committee meets once a year and reports the results of its deliberations to the Group Management Meeting, which is attended by directors and other officers of Nisshin Seifun Group Inc.
The Health and Safety Management Committee plays a central role in the implementation of PDCA cycles relating to occupational health and safety management under the Health and Safety Management Policy. We are particularly aware of the necessity of risk assessments as the “D” stage of the PDCA cycle, and we monitor the implementation of these assessments by group companies in Japan and overseas through audits conducted by the Health and Safety Management Department of Nisshin Seifun Group Inc. We also recognize the importance of audits from an external perspective, and we have been using third-party organizations to carry out assessments since fiscal 2016.

Preventing occupational accidents through risk assessments*
We introduced risk assessment activities and expanded them across the Nisshin Seifun Group in fiscal 2006. These activities now form a permanent part of operations at all of our production and research facilities.
In fiscal 2017, we further enhanced our overall activities by introducing chemical substance risk assessments at the relevant business sites. Before starting new projects, including mergers and acquisitions, we implement prior checks of the safety management and occupational safety systems of the target companies, including their responses to directives from labor-related authorities concerning corrective actions.
* A risk assessment is the overall process through which risk levels are assessed and risk tolerances are determined.
Occupational accidents in fiscal 2024
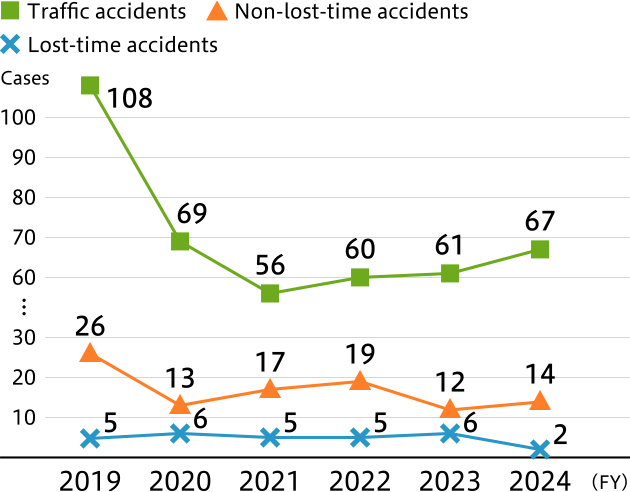
There were 14 non-lost-time accidents and two lost-time accidents in fiscal 2024. The number of lost-time accidents was reduced by four from the previous year’s total of six, but the number of non-lost-time accidents increased by two from the fiscal 2023 total of 12.
The number of trapping and entanglement accidents and the number of tripping accidents were unchanged from the previous fiscal year at three and two respectively. There were 11 other types of accidents, including four resulting from cutting and grazing, and two involving from collisions.
About 60% of accidents occurred when workers were performing routine tasks, and 40% when they were carrying out unexpected and non-routine tasks. We are taking steps to improve working environments and create workplaces in which the potential for accidents is low by ensuring that employees carry out hazard prediction and pointing and calling before starting any work activity, continually collecting information about near-misses, and encouraging risk assessment activities. Other accident reduction initiatives include safety education and countermeasures for older workers, who tend to be more accident-prone because of their declining physical capabilities. There have been no fatal accidents involving employees of the Nisshin Seifun Group for over 30 years.
Type of accident | FY 2022 | FY 2023 | FY 2024 |
---|---|---|---|
Trapping/entanglement | 5 | 3 | 3 |
Falls | 2 | 2 | 2 |
Others | 16 | 13 | 11 |
Scope: Direct or temporary employees (excluding part-timers) working for Nisshin Seifun Group Inc., Nisshin Flour Milling Inc., Nisshin Seifun Welna Inc., Nisshin Pharma Inc., Nisshin Engineering Inc., Oriental Yeast Co., Ltd., and NBC Meshtec Inc. (excluding subsidiaries and overseas business sites)
FY 2022 | FY 2023 | FY 2024 | |
---|---|---|---|
Nisshin Seifun Group*2 | 1.43 | 1.75 | 0.57 |
All industries in Japan | 2.09 | 2.06 | 2.14 |
All manufacturing industries in Japan | 1.31 | 1.25 | 1.29 |
*1 LTIR = The number of injuries and fatalities resulting from industrial accidents*/the total number of hours worked x 1,000,000
(* Injuries that result in one or more lost work days, and accidents and injuries that cause the loss of a body part or function are included.)
*2 Scope: Direct or temporary employees (excluding part-timers) working for Nisshin Seifun Group Inc., Nisshin Flour Milling Inc., Nisshin Seifun Welna Inc., Nisshin Pharma Inc., Nisshin Engineering Inc., Oriental Yeast Co., Ltd., and NBC Meshtec Inc. (excluding subsidiaries and overseas business sites)
The number of traffic accidents increased by around 10% over the previous fiscal year’s total. Just under 25% of accidents were caused by Nisshin Seifun personnel or by inattention by both parties, while just over 40% were self-inflicted. Most self-inflicted accidents resulted from collisions in parking lots, while many of the accidents caused by other parties involved rear-end collisions with stationary vehicles, such as vehicles stopped at red signals or in traffic jams. There were also accidents in which vehicles collided with pedestrians crossing roads at green lights. We remind people about the need to check their surroundings even when the light is green.
Initiatives to reduce traffic accidents include hazard prediction programs using videos, and the installation of dashboard cameras, safety devices, and driver support systems. Information about accidents is shared across the group. For example, at business sites where employees have been involved in traffic accidents, we analyze the causes and propose countermeasures in reports, which are continuously distributed throughout the group after checking and the addition of comments by the Health and Safety Management Department.
Occupational health and safety activities
We implement audits based on our own health and safety standards at domestic and overseas business sites of the Nisshin Seifun Group. When accidents occur, we work to prevent recurrences by informing all workers about the locations, circumstances, and causes of accidents and any countermeasures implemented. We also send engineers and production staff from the parent company to ensure that safety standards are rigorously applied at overseas subsidiaries.
Preventing serious injuries caused by trapping and entanglement in machinery
In fiscal 2023, a total of three workers were injured due to trapping and entanglement in machinery. This is the same as the number for the previous fiscal year. Accidents are still occurring when people’s hands become trapped in moving parts of machines while attempting unaccustomed tasks, such as repairing machines, that are in operation. Accidents are particularly likely to occur when people are engaged in non-routine activities that are different from their normal tasks. We are striving to prevent recurrences by ensuring that workers always switch off machinery before working on it, and by implementing hardware-related countermeasures, such as risk assessments of the machinery used and modifications to prevent hand trapping accidents. We are also improving our software, including the revision of operator manuals, the display of warning signs, the promotion of hazard prediction activities, and the provision of safety education. We are also sharing information about work processes and countermeasures across multiple work sites.
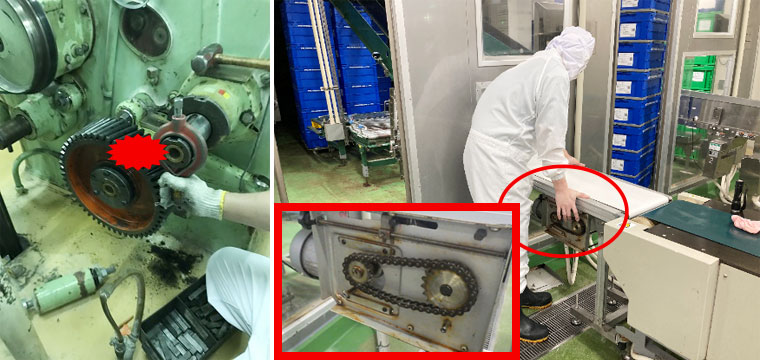
Occupational health and safety training
We implement a range of health and safety training programs for employees of our main group companies and their subsidiaries in Japan. The purpose of these programs, which are structured according to employee seniority, is to share our philosophy on health and safety with employees and provide environments in which people can work with confidence. The main programs are listed below.
Name and content of program | Targets | Number of attendees | ||
---|---|---|---|---|
FY 2022 | FY 2023 | FY 2024 | ||
Training for employees responsible for safety This program is for worksite health and safety activity leaders. Participants share and exchange information about ways to improve health and safety at business sites. (One one-day course) |
Health and safety activity leaders | 19 | 17 | 13 |
Supervisor safety training This course is designed to improve the skills of team leaders of business sites and employees who perform equivalent supervisory functions. (One three-day course) |
Team leaders and employees who perform equivalent supervisory roles | 18 | 40 | 42 |
Safety manager training The purpose of this course is to improve the skills of business site safety managers and employees performing equivalent safety management and supervision roles in organizations. (One two-day course) |
Safety managers and employees performing equivalent roles | 0* | 13 | 12 |
Follow-up safety training for supervisors This program is provided to enable supervisors to update their training after a certain number of years. (One two-day course) |
Team leaders and employees who perform equivalent supervisory roles | 0* | 15 | 16 |
Safety training for new employees (skilled workers) This program provides initial safety training for newly recruited skilled factory workers. (One half-day course) |
Newly recruited skilled workers | 46 | 56 | 62 |
Safety training for participants in technical skill improvement programs This program is designed to improve the safety-related skills of participants in technical skill (facility maintenance, analysis, etc.) improvement programs. (About two-hours per training program) |
Participants in technical skill improvement programs | 88 | 65 | 80 |
* Currently cancelled due to COVID-19
In addition to the above, we provide on-site participatory training in the prevention of trapping and entanglement accidents in response to requests from group companies.
In-house awards
Awards are presented to plants, research facilities, and business units that achieve excellent safety records, including zero lost-time accidents, serious traffic accidents, or fires.
- Zero Accident Awards
- Scope: Business sites that record three or more accident-free years in succession (Excellent Business Sites) or two accident-free years in succession (Improving Business Sites)
- Accident-Free Hours Award
- Scope: Business sites that achieve 500,000 working hours without accidents
FY 2022 | FY 2023 | FY 2024 | |
---|---|---|---|
Zero Accident Awards (Excellent Business Sites) | 9 | 11 | 15 |
Zero Accident Awards (Improving Business Sites) | 3 | 6 | 2 |
Accident-Free Hours Award | 2 | 4 | 4 |
Scope: Business sites of Nisshin Seifun Group Inc., Nisshin Flour Milling Inc., Nisshin Seifun Welna Inc., Nisshin Pharma Inc., Nisshin Engineering Inc., Oriental Yeast Co., Ltd., and NBC Meshtec Inc. (excluding subsidiaries and overseas workplaces)
Capacity building for subcontractors and other partners (Nisshin Engineering Inc.)
- We have established an Accident Prevention Council made up of persons responsible for coordination and management at individual construction sites with the aim of contributing to the prevention of accidents affecting frontline construction workers. As members of the Accident Prevention Council, both Nisshin Engineering and other concerned parties, such as subcontractors, ensure that health and safety initiatives are implemented proactively.
- The Accident Prevention Council holds meetings at least once a month to discuss matters relating to industrial accident prevention activities, such as worksite patrols, work-related communication and coordination, and various events relating to health and safety. Workers are informed about the content of these meetings.
Safety requirements for subcontractors (Nisshin Engineering Inc.)
- Before subcontractors or other parties enter worksites for the first time, their staff are provided with training on matters relating to health and safety.
- Safety-related compliance requirements
- Safety countermeasures based on the nature of the work that they will be performing
- Emergency actions and communications
- Nisshin Engineering has also created the Work Management Standards for Project Partners. These standards stipulate structures to ensure safe, efficient work management, cycles for safety-related actions, matters relating to work management, and accident reporting.
Infection prevention
As part of our commitment to fulfilling our supply responsibilities as a food manufacturer, we continually implement precautions against COVID-19 and other infectious diseases and issue procedures to be followed in the event that infections occur. Depending on the circumstances, actions to prevent the spread of infections include the establishment of a task force, the issuance of notifications to all employees, and the establishment of clearly defined reporting lines.
Our business activities are becoming increasingly global in scope. Employees transferred to our overseas business operations receive guidance in the prevention of malaria, which is prevalent in Southeast Asia, and other infectious diseases. We have established an Overseas Medical Assistance System to introduce medical institutions and arrange treatment for employees who are affected by accidents or illness, including infectious diseases.